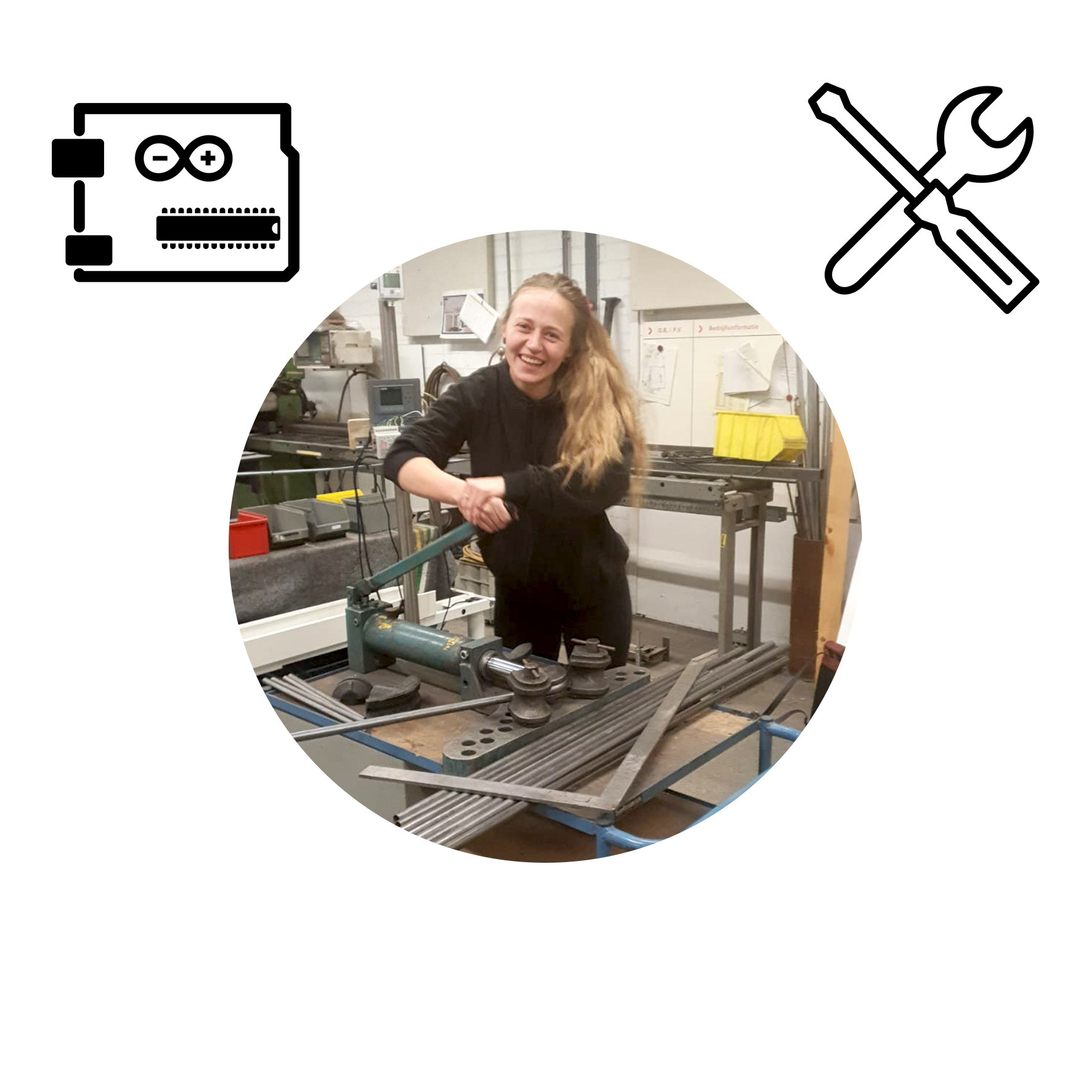
This expertise area was completely undeveloped for me, or at least that is how I felt at the beginning of the program. I did not have any prior experience in building Arduino circuits or programming for it, as my Bachelor's was focused more on traditional technological aspects.
This previous knowledge turned out to be very useful in building Reload Booth with Ahrend. Due to my capability of creating technical drawings from the Fusion 3D model, I was able to communicate my ideas quickly and build the furniture based on them. It was the first time I used my drawings to build any physical prototype. The process gave me a lot of insight into how to prepare those documents to navigate easily and prevent mistakes in production.
In my Bachelor, I was presenting ideas mostly using 2D visualization, so building large-scale demonstrators was a challenge for me. I am glad that I decided to create a 1:1 prototype of Momentum chair as it gave me the confidence to push it even further. To assemble it easily in my own apartment I created drawings in AutoCad for CNC milling of the plywood and use finger joints as a connection between plates. This way I gained experience working with wooden elements. I got interested in designing furniture and it influenced the choice of company for my Internship in M21 semester. During my cooperation with Ahrend, I spent a lot of time in the workshop not only building my own prototype, but also learning how other products are developed and constructed. In the end, I created furniture with canopies made from bent steel pipes, and wooden arms of the armchair made from plywood.
In terms of implementing interaction and electronics in the demonstrators, I certainly developed a lot. During M12 project I started to learn very basics of Arduino. This semester I used vibration motors to indicate the time to turn the chair and various vibration patterns to create a personality of Momentum. In the next prototype, I overridden the controls of the actuator from a reclining chair (used for Reload Booth) and added a pressure sensor to make the interaction automated. In the Miural demonstrator, I have implemented speakers, a sound sensor and servomotors to move the fabric whenever the noise level rises significantly.
Learning to build and program electronics was certainly a difficult process, but I saw potential in testing the actual interactions of the product and the importance of defining it in the early stages of development.
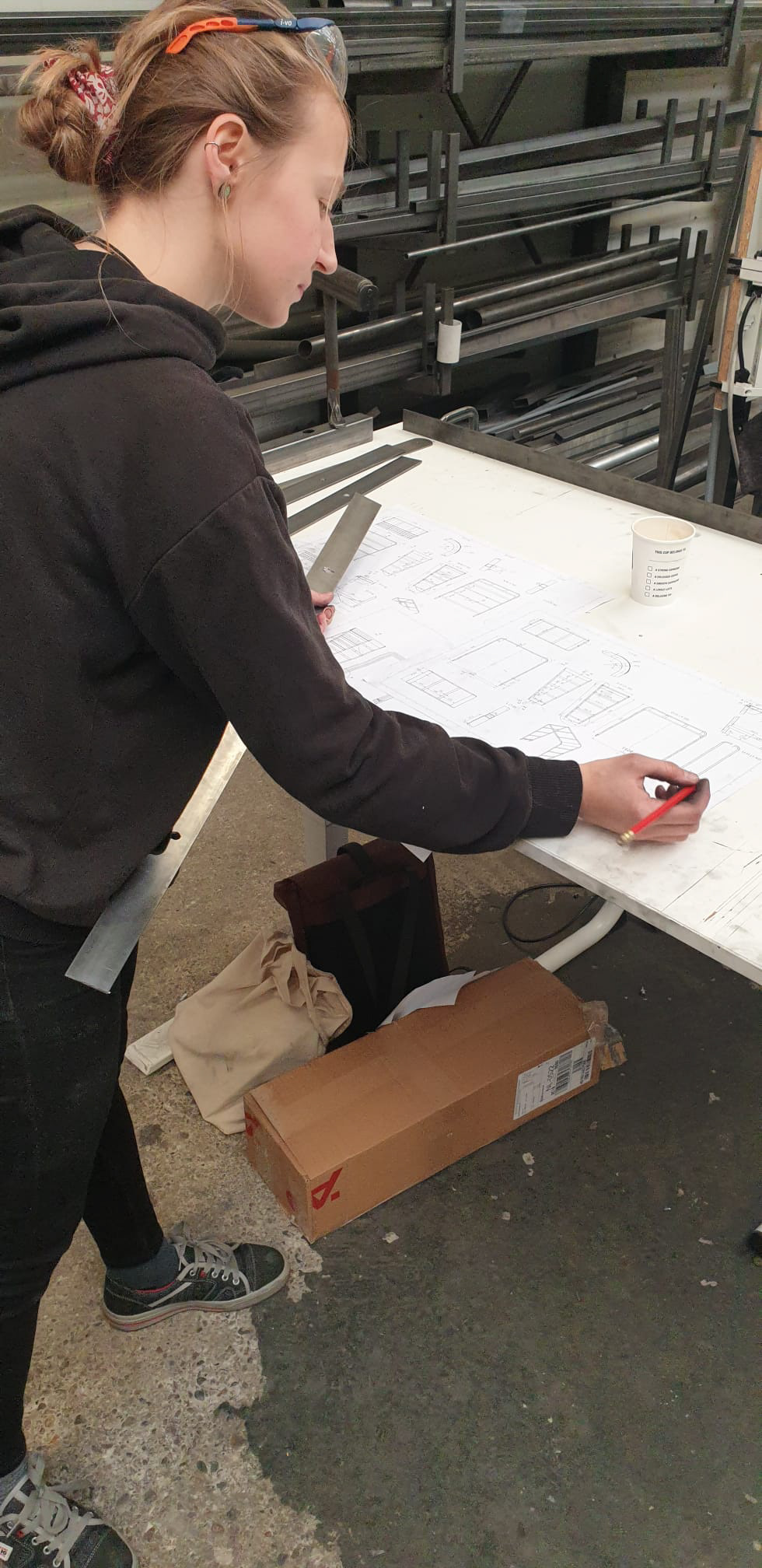
Reading technical drawing (M21)
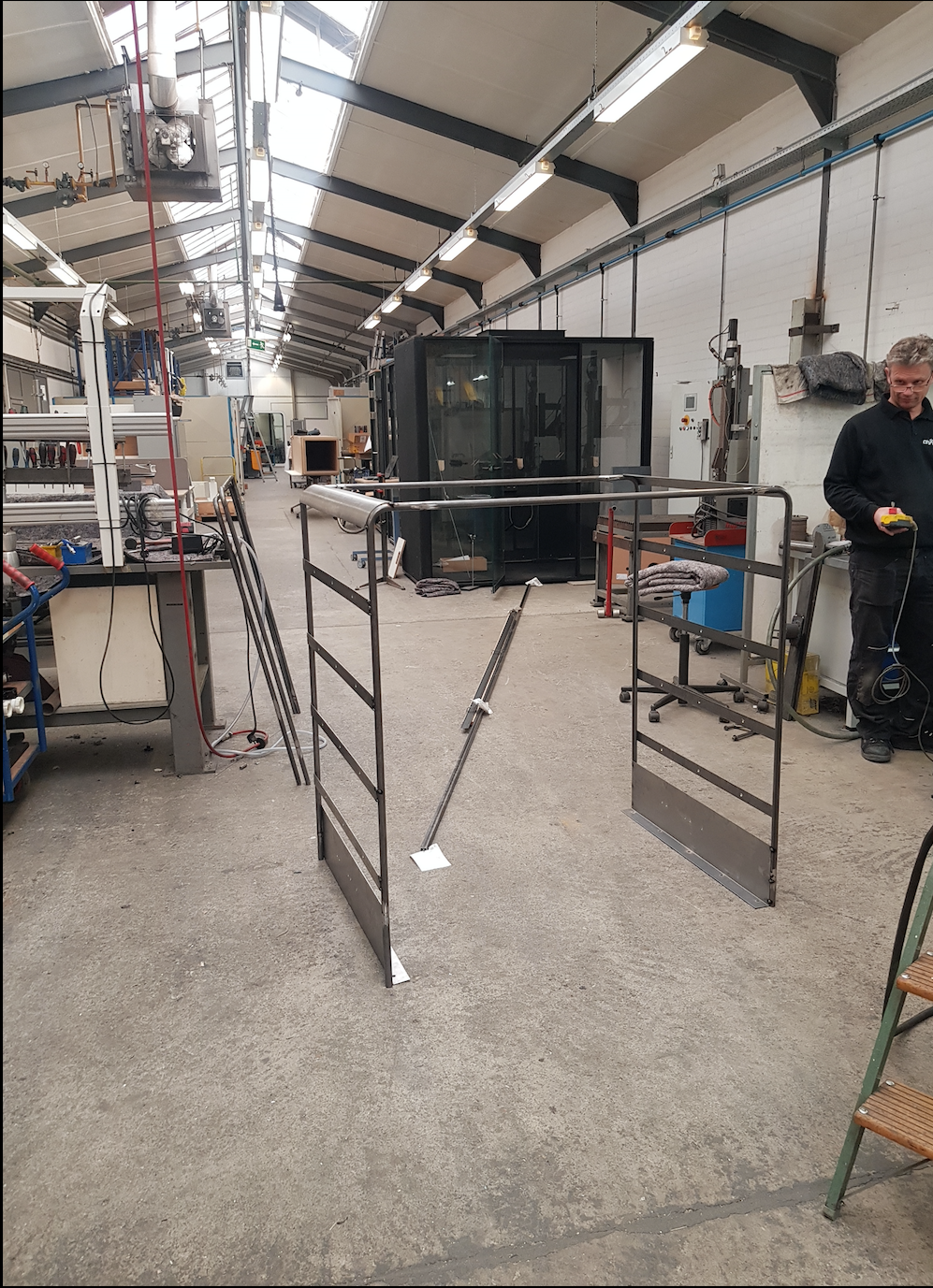
Steel structure of the canopy (M21)
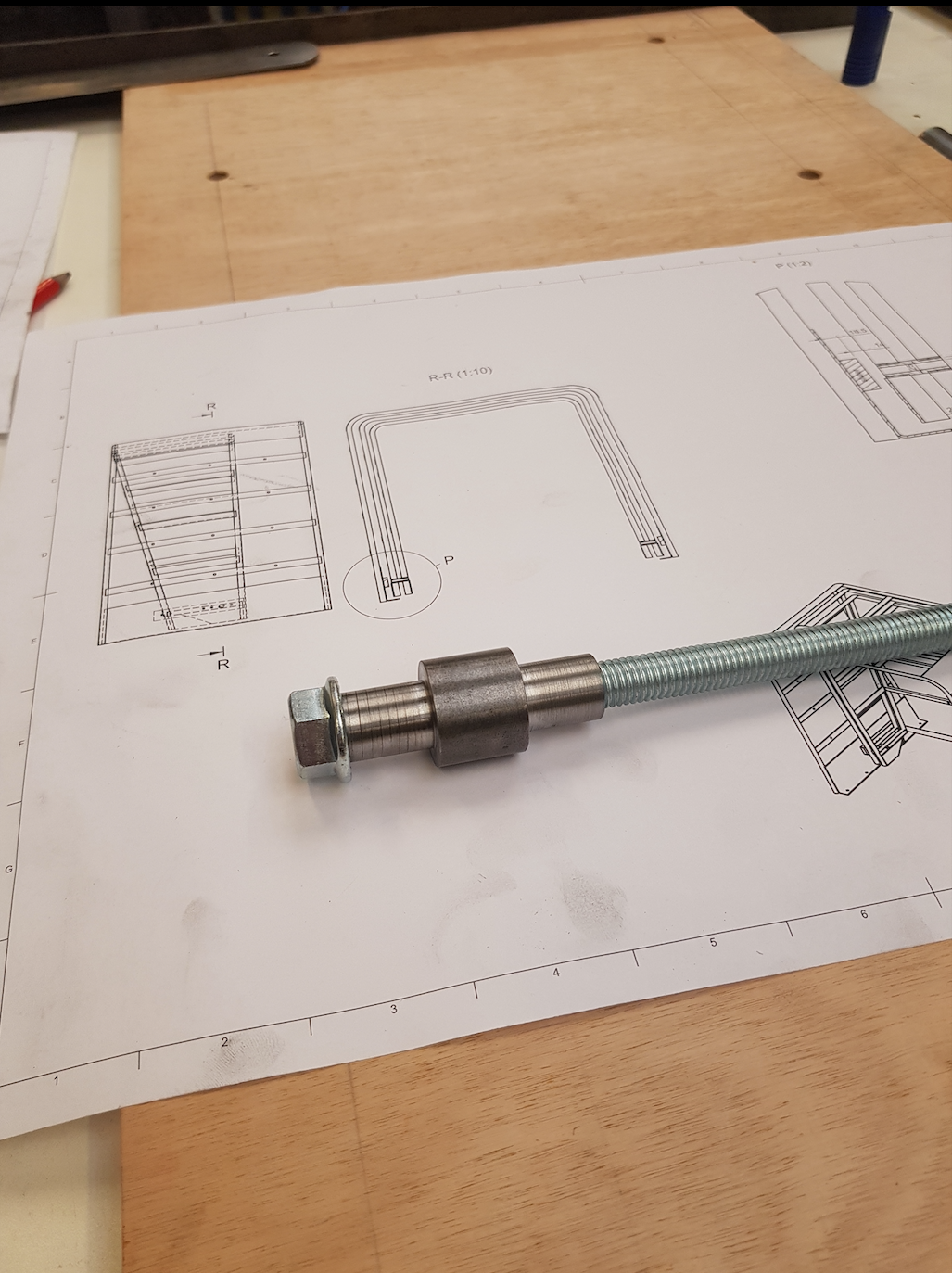
Pivot point of the canopies (M21)
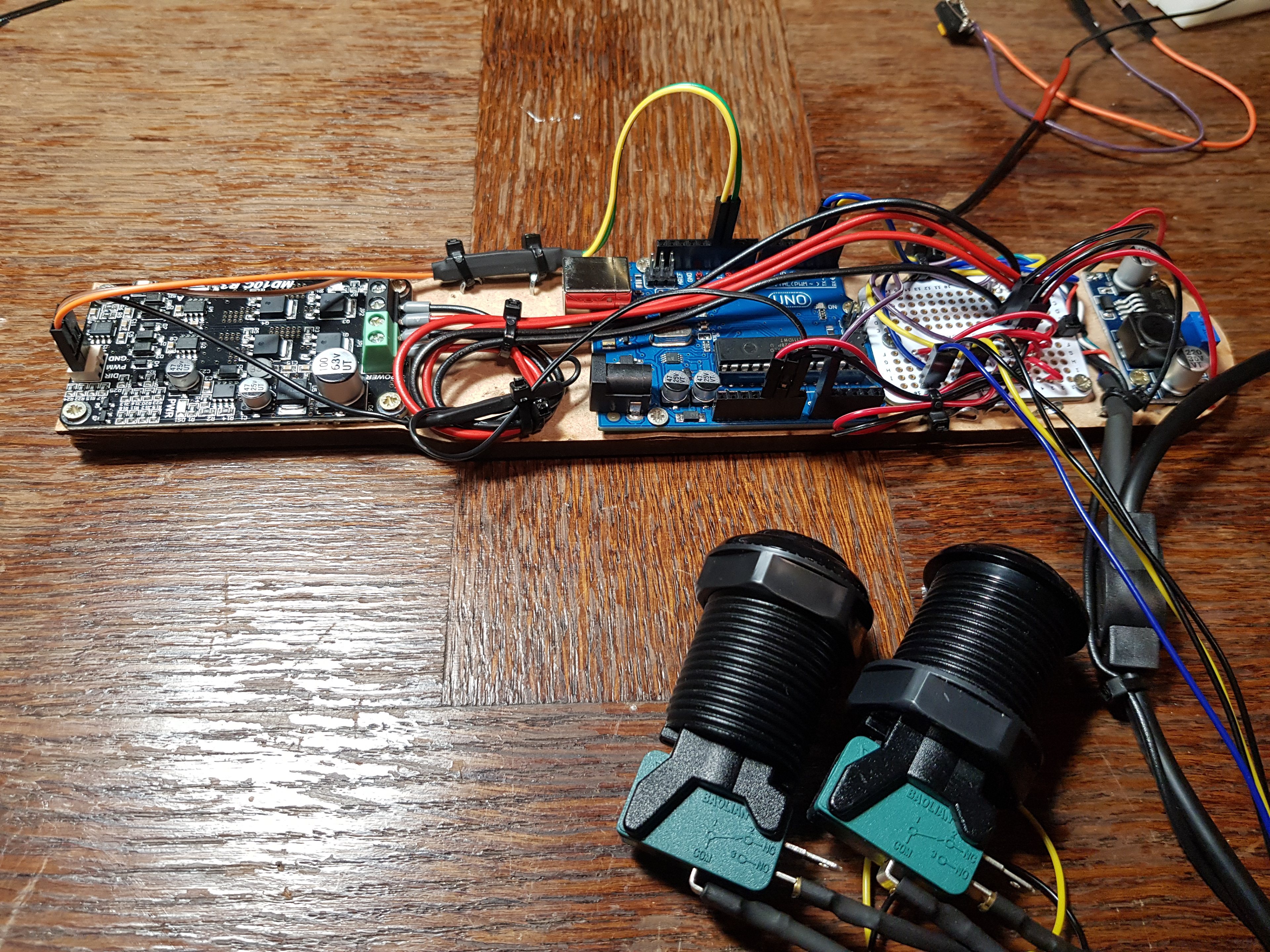
Electronics to control actuator (M21)
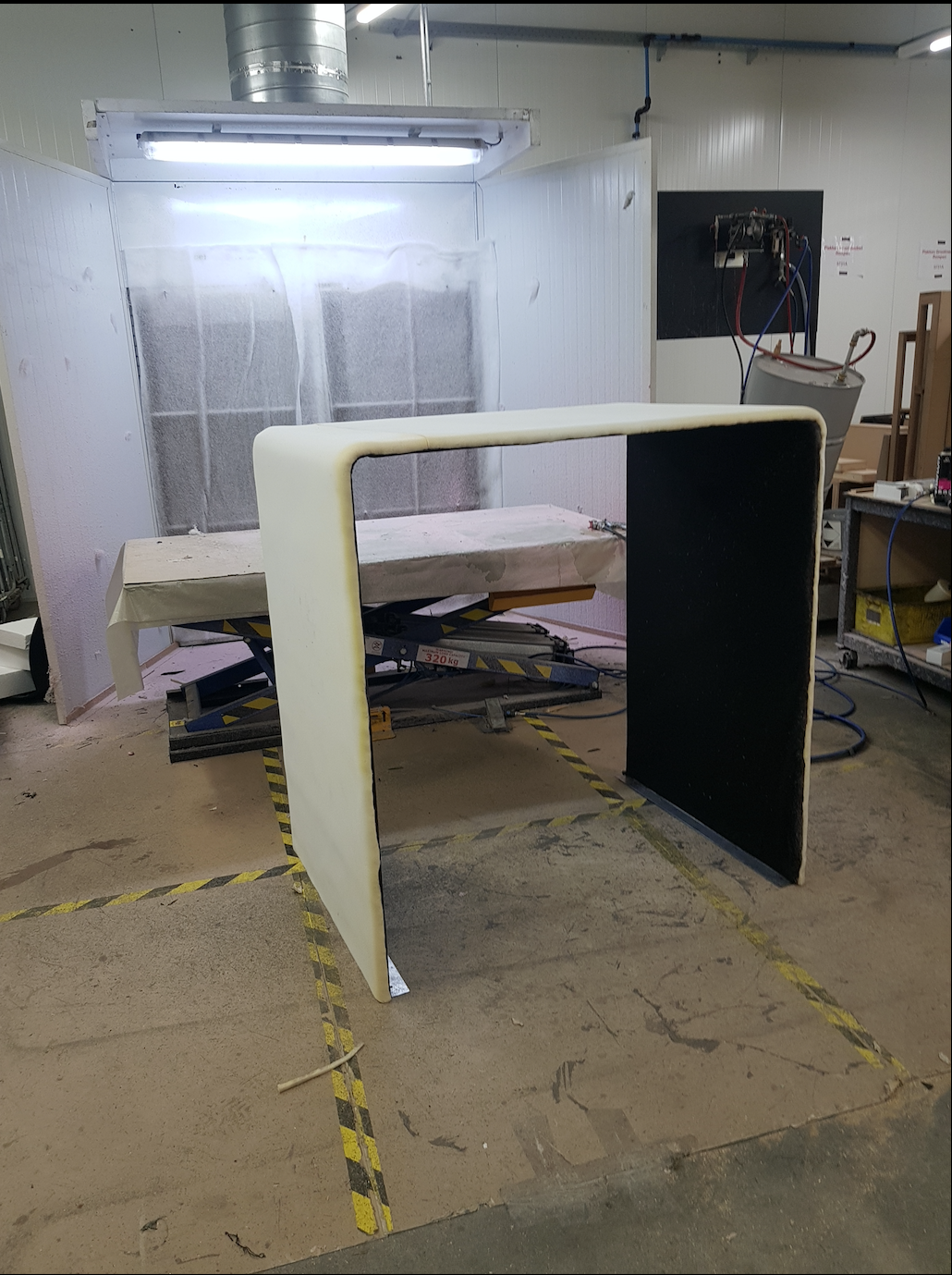
Canopy ready for upholstery (M21)
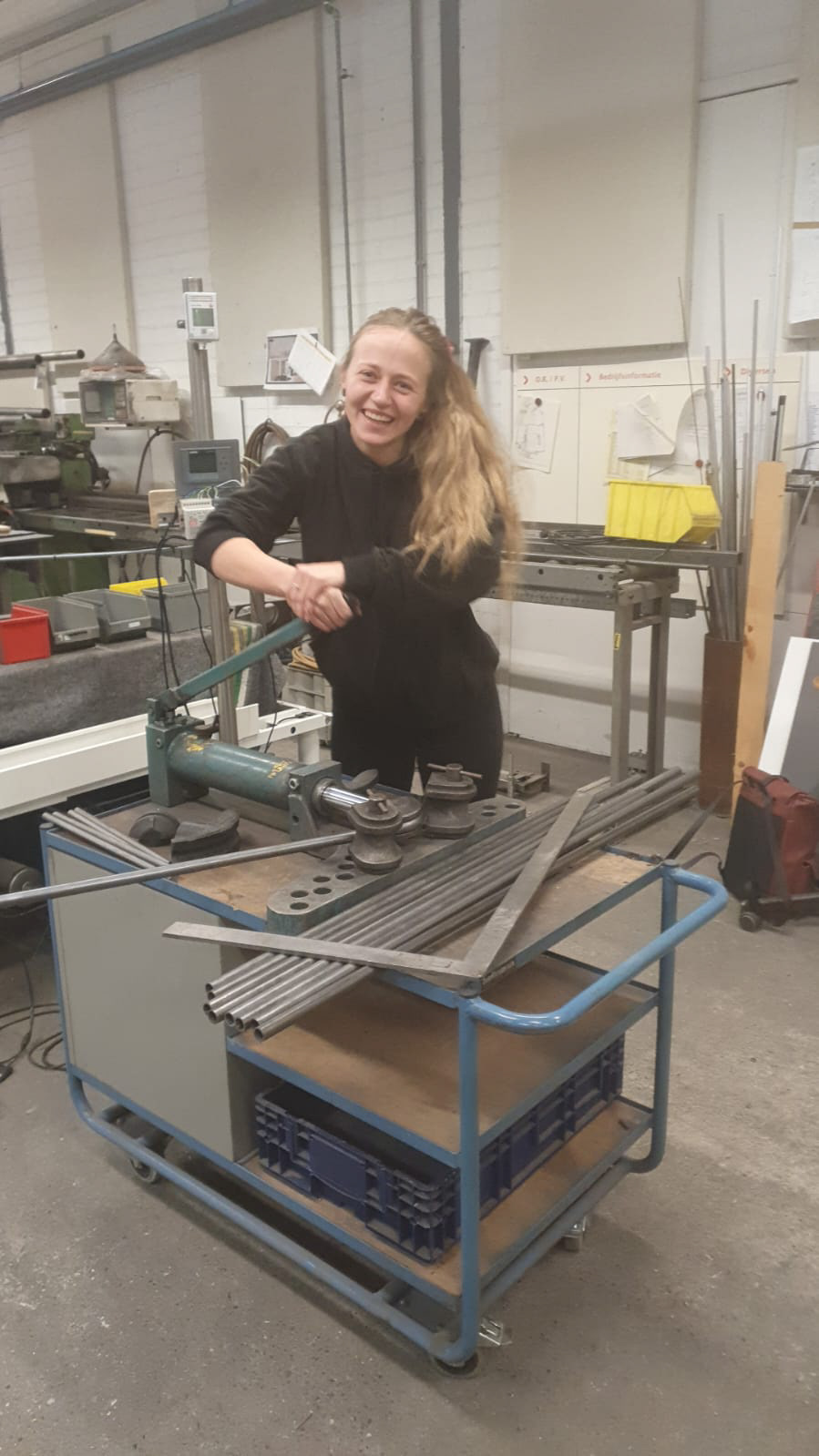
Bending steel pipes (M21)
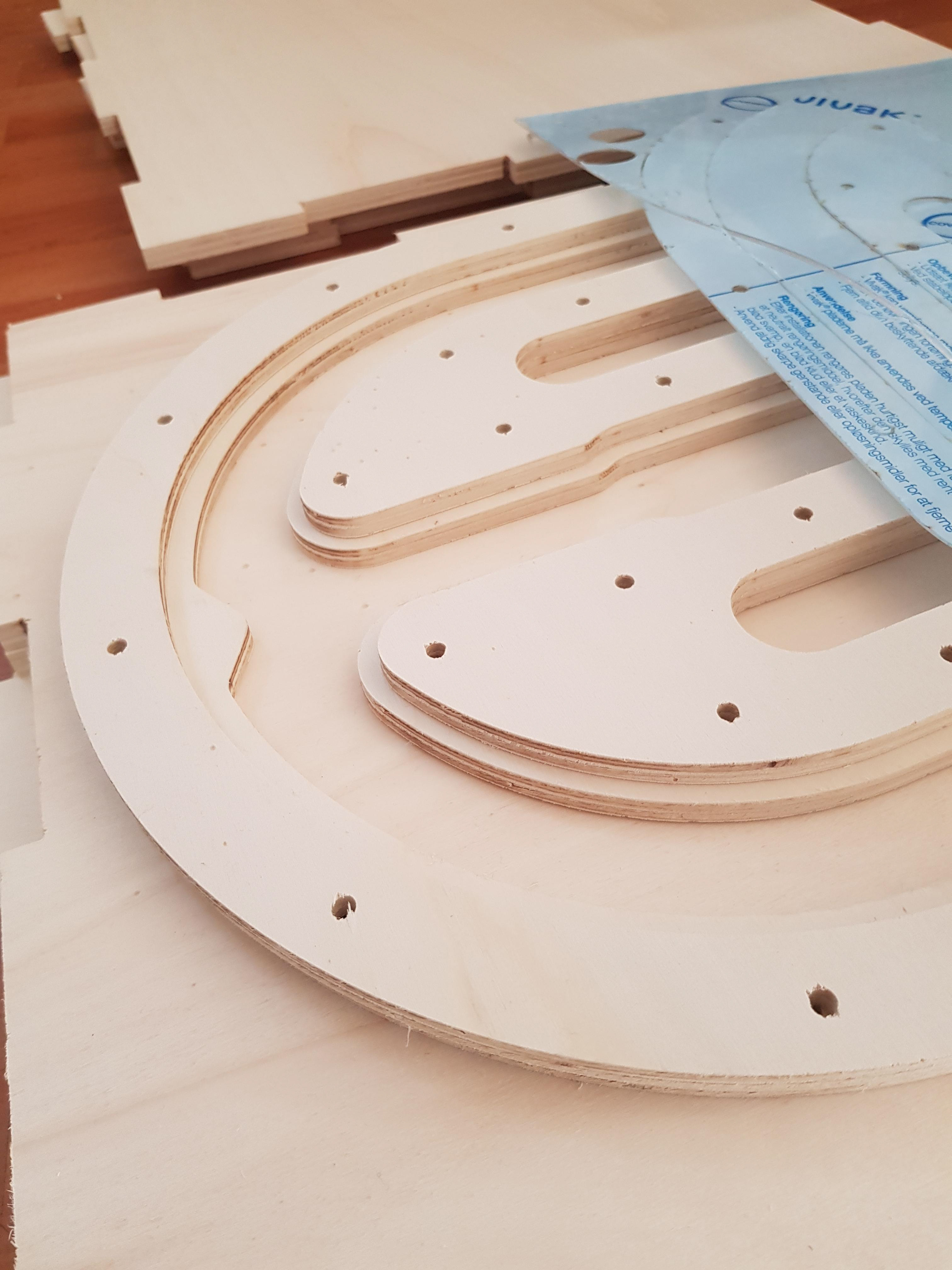
Turning mechanism of Momentum (M12)
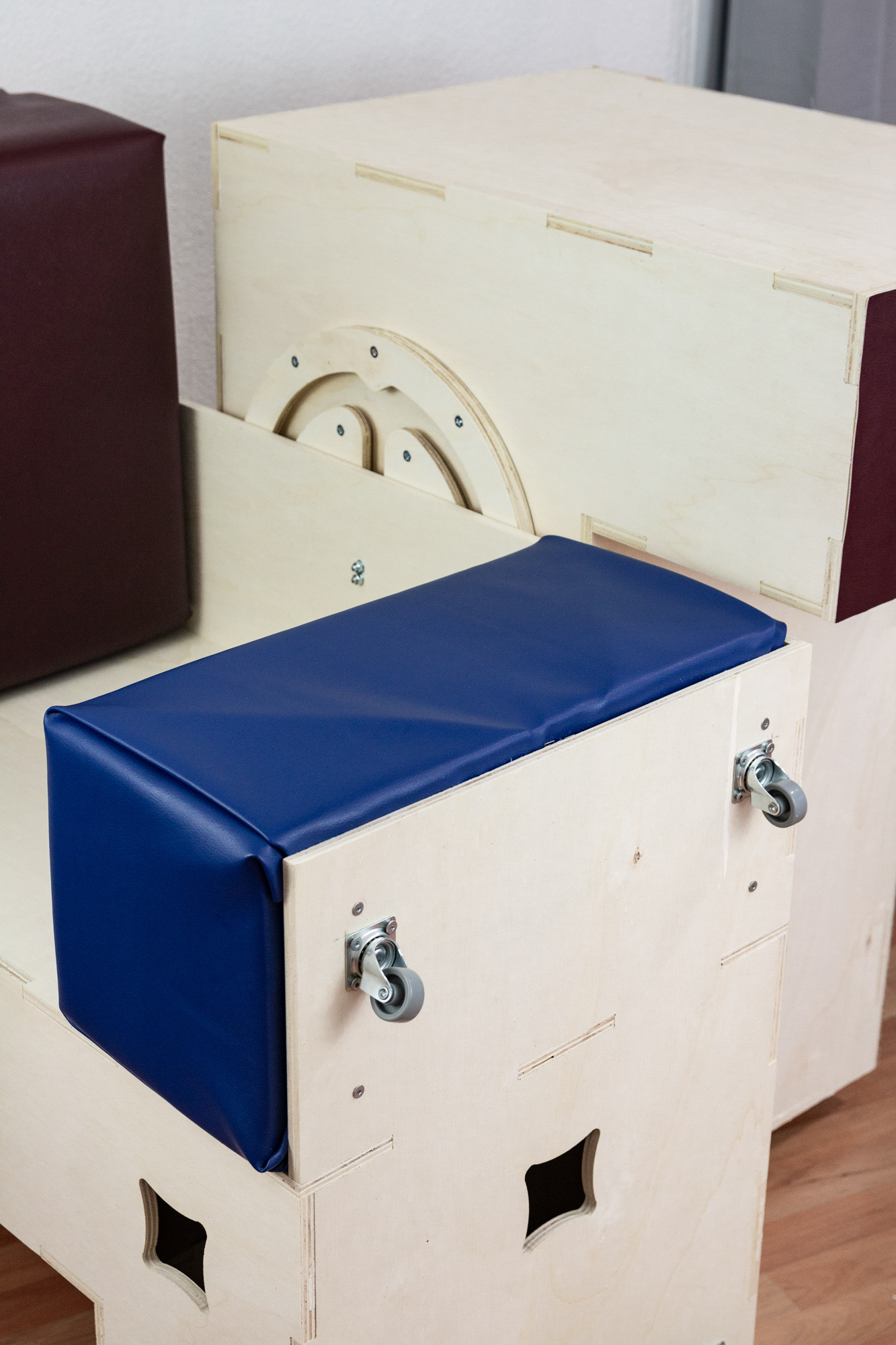
Technological details - finger joints (M12)
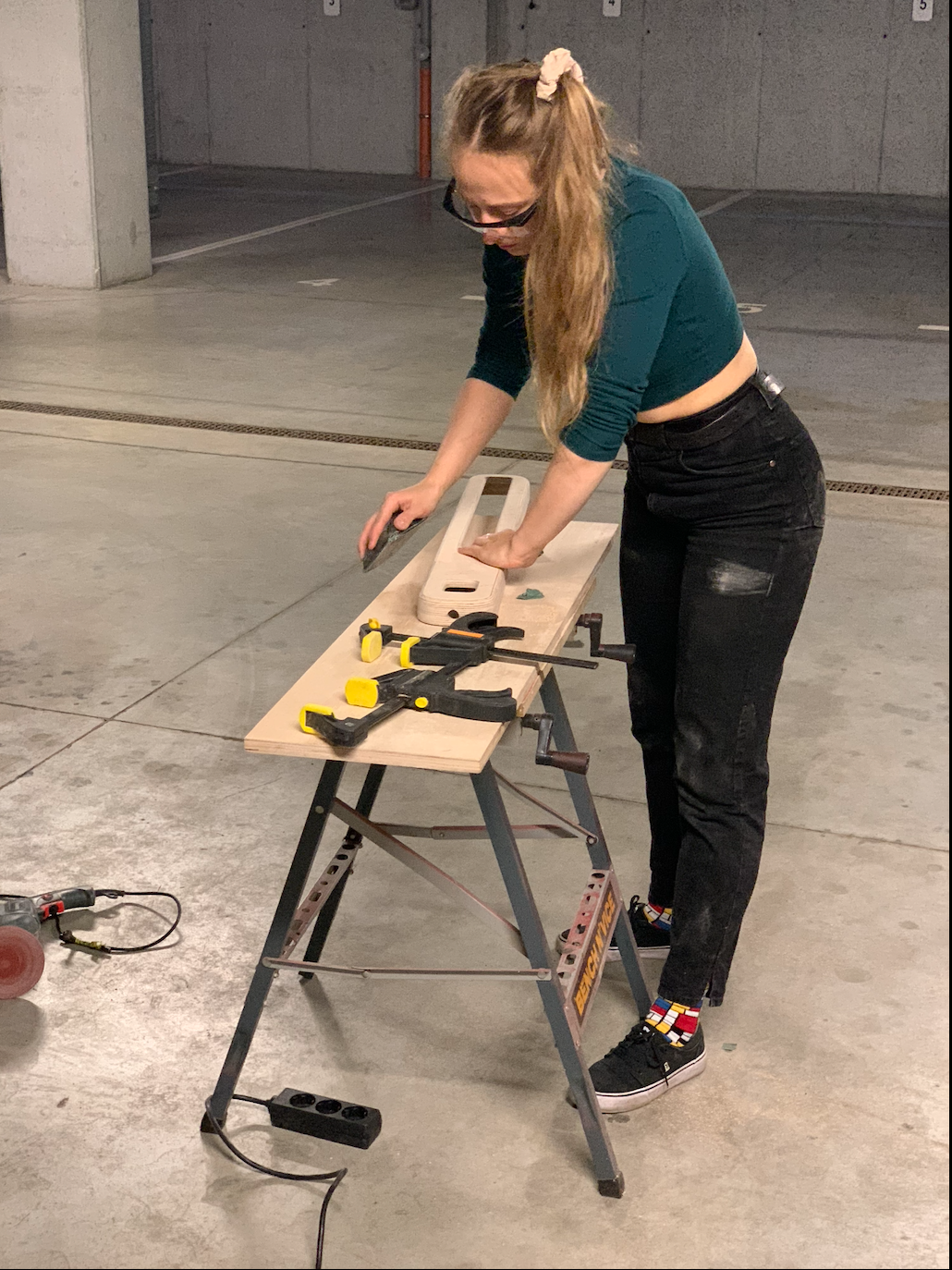